Focos de atención
Soldador de línea de montaje, Soldador, Soldador de fabricación, Soldador de mantenimiento, Soldador MIG (Soldador de gas inerte metálico), Soldador, Soldador TIG (Soldador de gas inerte de tungsteno), Soldador, Montador de soldadura, Alicatador, Cortadores y montadores
Imagine a world without bridges, skyscrapers, or even cars. What do all these things have in common? They rely on the skill and precision of Welders to put them together!
Welders are the backbone of countless industries we rely on. They bring blueprints to life by transforming raw materials into finished products, building the metal frameworks for everything from heavy machinery to towering structures and vehicles used on air, land, and sea.
Welders are trained to safely work with dangerous tools (such as torches, electric arc machines, plasma cutters, and grinders) to join, cut, and shape metal parts. With ~30 different types of welding ranging from basic to advanced and specialized, there is a technique suited for nearly every application and industry need.
If you enjoy working with your hands, solving problems, and creating things that are built to last, you might be cut out for a career in welding!
- Creating and repairing critical structures and components
- Working with advanced tools and technologies
- Being part of a highly skilled and respected trade
- Opportunities to work in diverse industries and environments
“In most situations where welding is involved, you’re in a position where you’re an integral link of a chain when working on projects,” writes Darrell Cates, welder and mechanic at Hall Fabrication and Racing in California.
“This allows you to showcase your skills as a welder and illustrates that the skills of a welder are just as valuable as other skills required to complete that project. This gives you a sense of self-satisfaction, a reward for being part of a team effort.”
Horario de trabajo
Welders typically work full-time, with the potential for overtime to meet deadlines. They may work in settings such as garages, factory warehouses, construction sites, and shipyards.
Tareas típicas
- Discuss project specifics with clients or managers, as needed.
- Select the appropriate welding method, equipment, and materials.
- Read and interpret blueprints, sketches, and technical drawings to understand project specifications.
- Lay out and position parts for assembly.
- Align and clamp workpieces together before welding.
- Prepare materials by cleaning, cutting, or grinding metal surfaces.
- Preheat or heat-treat metal parts to remove stresses and prepare materials.
- Weld components in flat, vertical, or overhead positions, as needed.
- Monitor and adjust heat, speed, or feed rates.
- Inspect welded surfaces and structures to ensure they meet quality standards and specifications.
- Test welded structures using visual inspections or other testing methods.
- Identify and troubleshoot defects and make repairs.
- Operate grinders, drills, or other tools to finish and smooth welded surfaces.
- Perform routine maintenance and calibration on welding equipment and tools.
Funciones adicionales
- Follow safety protocols and wear personal protective gear.
- Collaborate with other tradespeople, such as pipefitters or fabricators, on joint projects.
- Train and supervise apprentices or junior welders.
- Stay updated on industry advancements and new technologies.
- Maintain records of materials, specifications, and modifications for welding projects.
- Implement quality assurance programs and ensure compliance.
- Fabricate custom parts or prototypes based on unique designs.
- Keep work areas clean and free from potential hazards.
- Support emergency repairs and post-weld treatments.
Note, the roles of Cutters, Solderers, and Brazers are closely related to Welders! They all work with metals and heat to shape, join, or dismantle materials, but their specific methods and applications set them apart.
For instance, Cutters specializes in separating and shaping metal components using high-temperature tools like plasma cutters, oxy-fuel torches, or laser cutters. Their role is important in fabrication and deconstruction (dismantling large structures such as ships, pipelines, or heavy machinery).
Solderers and brazers, on the other hand, focus on joining metal components. Solderers typically work at lower temperatures to bond small, delicate parts, making their skills essential in fields like electronics and jewelry manufacturing.
Meanwhile, Brazers use higher temperatures to join dissimilar metals, creating strong, corrosion-resistant bonds suitable for products that endure wear or harsh environments. Brazers also coat components to enhance durability and performance.
Together, all of these distinct but related professions form an essential part of metalworking industries!
Habilidades blandas
- Capacidad para trabajar de forma independiente
- Adaptabilidad
- Atención al detalle
- Pensamiento crítico
- Destreza
- Flexibilidad
- Destreza manual
- Organización
- Persistencia
- Resolución de problemas
- Ingenio
- Conciencia de seguridad
- Buen juicio y toma de decisiones
- Fuerza y resistencia
- Gran capacidad de comunicación
- Trabajo en equipo
- Gestión del tiempo
- Visualización
Habilidades técnicas
Welders require technical skills related to the following areas:
- Blueprints/technical diagrams
- Computer-aided design (CAD) software (e.g., AutoCAD, SolidWorks)
- Emergency and safety equipment
- Fabrication layout tools (e.g., laser alignment systems, precision measuring instruments)
- Heat and temperature monitoring tools (e.g., infrared thermometers, pyrometers)
- Material property analysis software
- Metallurgy and material properties
- Non-destructive testing software
- Simulation software for welding processes (e.g., Simufact Welding, ANSYS)
- Soldering techniques
- Surface preparation and finishing equipment (e.g., sanders, abrasive blasting tools)
- Welding automation systems (e.g., robotic welding arms, programmable logic controllers)
- Welding documentation and certification tracking
- Welding inspection and quality control
- Welding and welding inspection software (e.g., WeldShop, WeldOffice, Hypertherm ProNest)
- Welding safety practices
- Welding techniques, depending on the role, include:
- Entry-level techniques:
- Advanced welding types:
- Specialized types of welding:
- Welding tools and equipment (e.g., grinders, torches, clamps)
- Industria aeroespacial
- Agricultural equipment industry
- Industria del automóvil
- Empresas de construcción
- Defense and military contractors
- Manufacturing plants
- Metal fabrication shops
- Mining operations
- Oil and gas extraction companies
- Pipeline construction and maintenance companies
- Power generation facilities
- Railroad maintenance and manufacturing
- Renewable energy sectors (e.g., wind turbine construction)
- Research and development labs
- Sculpture studios
- Shipbuilding and repair facilities
Welders must consistently deliver high-quality, durable welds that adhere to rigorous safety and industry standards. This requires a commitment to precision and skill because even small imperfections can compromise structural integrity.
The job can entail long hours, repetitive tasks, and tight deadlines, especially in industries like construction and manufacturing. In addition, working conditions can be challenging, with some tasks performed in confined spaces, at great heights, or under extreme temperatures.
Welding frequently involves exposure to intense light, fumes, and sparks, making personal protective equipment and adherence to safety protocols essential. There may also be some heavy lifting and long periods of standing or crouching involved.
In terms of schedules, Welders might have to work night shifts or weekends, or may be asked to travel for specialized projects. These sacrifices can take a toll on work-life balance, especially for those who work in industries such as shipbuilding, pipeline construction, or aerospace manufacturing and maintenance where they might be far from home.
Technological advancements are transforming the welding industry, with automation and robotics leading the way. For example, robotic welding systems continue to revolutionize production lines, especially in high-volume sectors like automotive manufacturing. Laser and friction stir welding are increasing the ability to join complex materials efficiently, enabling Welders to concentrate on other tasks.
Eco-friendly techniques such as low-emission flux-cored wires and solar-powered welding machines are gaining traction, too. Many companies are even adopting materials recycling practices and energy-efficient processes to reduce their carbon footprint while maintaining standards of quality.
As the industry evolves, Welders can keep up with these emerging technologies and methods by taking professional development courses. Training in robotic welding, non-destructive testing, advanced metallurgy, and other modern topics can help to ensure workers stay competitive and can access more opportunities for career advancement.
“Welding in space is the current leading edge that’s pushing advancements. And industrial construction is always improving methods and procedures, pushing the industry forward.” - Darrell Cates
Welders often enjoyed hands-on activities, such as building models, working on cars, or engaging in metalworking hobbies. They likely had an affinity for precision tasks and problem-solving, as well as a fascination with how things are constructed and repaired.
“Welding skills have a very wide application. That gives a broad potential spectrum to any “day in the life” for a welder. For example, you could be a benchtop welder working 8 am - 5 pm, 40 hour weeks. Or maybe a pipeliner doing 15-hour days, six days a week. Or perhaps an underwater welder working 30 days on and 60 days off, welding for six hours underwater (which takes 12 hours to make that happen). Lots of options!” - Darrell Cates
- Welders need at least a high school diploma or equivalent. Courses in math, science, and shop during high school provide a helpful foundation.
- Completing a formal welding training program at a vocational school, community college, or technical institute is beneficial and looks good on a job application.
- Some employers provide full on-the-job training via apprenticeships working under the guidance of an experienced Welder.
- Common education and training topics include:
- Basic and advanced welding techniques
- Lectura de planos
- Cutting techniques
- Heat control and distortion management
- Joint design and preparation techniques
- Metallurgy
- Shielding gases
- Solución de problemas
- Types of welds
- Welding automation and robotic systems
- Welding codes and standards
- Welding safety
- Welding symbols and terminology
- Students may learn specialized welding techniques (e.g., pipe welding, underwater welding, aluminum and stainless steel
welding), advanced processes (like laser welding and electron beam welding), and welding in specific environments (such as high-pressure, high-heat, or hazardous conditions). - Optional certifications offered by the American Welding Society or other organizations are often desired by employers. Options include:
- Certified Associate Welding Inspector
- Certified Resistance Welding Technician
- Soldadura por arco robotizada certificada
- Certified Welder Program
- Certified Welding Engineer
- Certified Welding Inspector
- Certified Welding Supervisor
- Welder Performance Qualification and Welder Certification
- Continuing education is vital to stay updated with new welding tools, techniques, and industry standards.
- Consider the cost of tuition, discounts, and local scholarship opportunities, in addition to federal aid.
- Make sure the program is reputable and has modern facilities and equipment. Also check out the program’s instructors and their backgrounds.
- Look for programs that offer lots of hands-on practice.
- Note, some courses are fine for online attendance, such as the American Society of Mechanical Engineers’ Practical Welding Technology – Virtual Classroom. But you’ll still need real-world practice to apply what you learn.
- See if the program posts job placement stats and connections with local employers.
- Read reviews from previous students or ask people on online forums.
- Take courses in mathematics, physics, and shop classes. If possible, sign up for welding-related community college or vocational classes while in high school.
- Some high schools will pay for these classes and allow you to get dual credit. Talk to your academic advisor!
- Get certified from the American Welding Society or take courses from the American Society of Mechanical Engineers.
- Participate in welding or metalworking clubs and competitions.
- Seek internships or part-time jobs where you can get on-the-job training and develop hands-on skills.
- Develop a portfolio showcasing your welding projects and skills.
- Watch welding-related videos on YouTube channels (like Weld.com’s channel) and educate yourself through welding books, welding magazines, and online articles.
- Ask a working Welder if they have time to do an informational interview with you.
- Decide what type of entry-level techniques you want to focus on learning, such as:
- Metal Inert Gas (MIG)
- Flux-Cored Arc
- Gas Metal Arc
- Oxy-Acetylene
- Resistance Spot
- Shielded Metal Arc
- Note, many employers in the skilled trades, including welding, conduct substance tests as a part of their hiring process to ensure a safe working environment. The use of welding equipment can be hazardous, so employers (and insurance companies) have to reduce risks.
“Things that are required to be in an advanced welding position would be math at a minimum, with advanced math preferred. Drawing and drafting by hand and computer, too. Physical fitness is also key because this field can be demanding.” - Darrell Cates
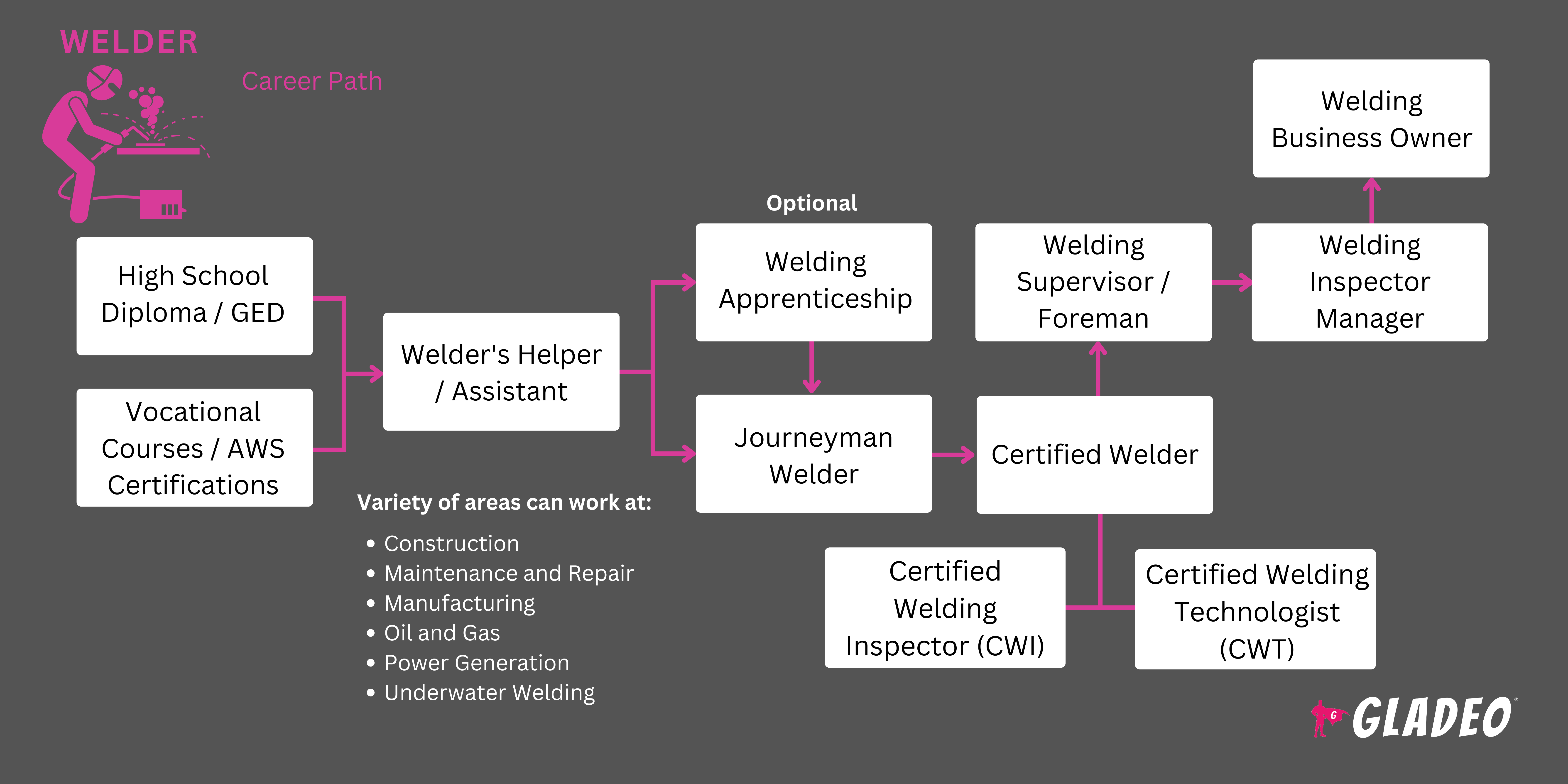
- Network with professionals in the welding industry and rack up as much relevant experience as you can in school or on your own.
- Websites like Glassdoor, Indeed, USAJOBS, Jobs In Welding, American Welding Society, or SimplyHired are good starting points for finding jobs. Look for apprenticeship opportunities at Apprenticeship.gov.
- Ask your school’s career services staff for help with resumes, mock interviews, and job searches. Reach out to your network to let them know you’re looking for work.
- Screen job ads carefully to ensure you meet requirements and have the right experience.
- Look for important keywords to work into your resume/application, like:
- Arc welding
- Lectura de planos
- Brazing
- Fabrication
- Grinding
- Metal cutting
- MIG or TIG welding
- Pipe welding
- Plasma cutting
- Safety compliance and quality control
- Structural welding
- Welding certifications (e.g., AWS, ASME)
- Welding equipment maintenance
- Welding inspection
- Review Welder resume templates to get ideas for formatting and phrasing.
- Engage in online forums and ask career advice questions.
- Brush up on your welding terminology.
- Ask your professors, supervisors, and peers if they’ll serve as personal references. Get their permission before you give out their information, though.
- Look up common Welder interview questions. Examples might include: “Can you describe your experience with different welding techniques, such as MIG, TIG, or stick welding, and provide examples of projects where you used them?” or “How do you ensure safety and maintain quality standards when working on a welding project?”
- Vístete siempre adecuadamente para tener éxito en la entrevista de trabajo.
- Talk to your supervisor about how you can progress. Let them know you are willing to knock out additional training they suggest.
- Find out if your employer is willing to cover or reimburse you for tuition costs for welding courses.
- Obtain American Welding Society certifications such as:
- Certified Resistance Welding Technician
- Soldadura por arco robotizada certificada
- Certified Welding Inspector
- Certified Welding Supervisor
- Learn advanced or specialized welding types such as:
- Gas Tungsten Arc Welding
- Plasma Arc Welding
- Submerged Arc Welding
- Thermite Welding
- Tungsten Inert Gas (TIG)
- Electron Beam Welding
- Explosion Welding
- Keep active in professional organizations to learn new things and grow your network.
- Challenge yourself to work on more complex projects.
- If necessary, apply for jobs that offer more advancement potential.
Páginas web
- American National Standards Institute (ANSI)
- American Welding Society (AWS)
- Fabricators & Manufacturers Association International (FMA)
- International Brotherhood of Boilermakers
- Ironworkers Local Union 29
- National Center for Welding Education and Training
- Society of Manufacturing Engineers (SME)
- The Fabricator
- United Association (UA) Welders
- United Association of Journeymen and Apprentices of the Plumbing and Pipefitting Industry (UA)
- Weld.com
- Welding Digest
- Welding Journal
- Welding Tips and Tricks
Libros
- Welding: Principles and Applications, by Larry Jeffus
- Modern Welding, by Andrew Althouse, et. al.
- Welding for Dummies, by Steven Robert Farnsworth
Welders play an important role in a wide range of crucial industries, but it can be a demanding job at times. For those considering alternatives, related careers include:
- Calderero
- Instalador de armarios
- Ebanista
- Programador CAM
- Carpintero
- Ceiling Tile Installer
- CNC Machinist
- Inspector de construcción y edificación
- Obrero de la construcción
- Instalador de paneles de yeso
- Electricista
- Flooring Installer
- Acabador de muebles
- Obrero de mantenimiento general y reparaciones
- Técnico de HVAC
- Mecánico de maquinaria industrial
- Aislador
- Montador de máquinas herramienta de torno y torneado
- Machinist
- Albañil
- Creador de modelos
- Instalador de tuberías
- Escayolista
- Techador
- Trabajador de chapa metálica
- Instalador de energía solar fotovoltaica
- Fabricante e instalador de estructuras metálicas
- Tile and Stone Setter
- Fabricantes de herramientas y matrices
- Woodworking Machine Operator
“Final thoughts are — this career is one that’s found around the world, on land and sea, in hot and cold, and indoors or out! It's difficult and hard work, but rewarding.” - Darrell Cates
Newsfeed
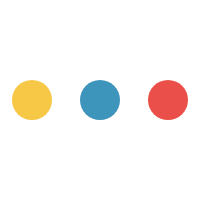
Trabajos destacados
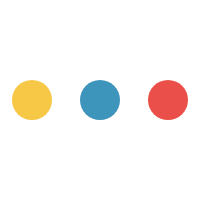
Cursos y herramientas en línea
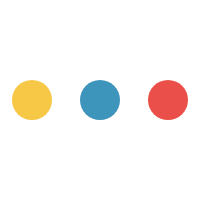